What Are the Costs Associated with Machinery Maintenance
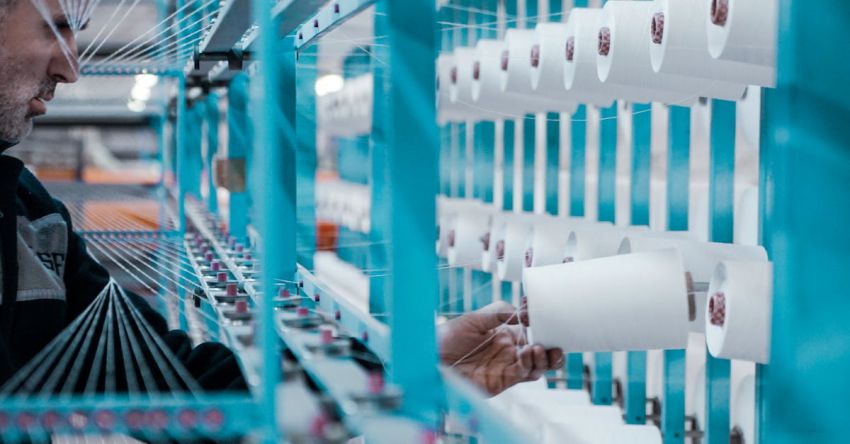
Machinery maintenance is a crucial aspect of any operation that relies on equipment to function efficiently. While the benefits of regular maintenance are well-documented, the costs associated with keeping machinery in top condition are often overlooked. In this article, we will delve into the various expenses that come with maintaining machinery and why investing in proper upkeep is essential for long-term success.
The Cost of Downtime
One of the most significant expenses related to machinery maintenance is the cost of downtime. When equipment breaks down unexpectedly, it can bring operations to a standstill, resulting in lost productivity and revenue. Moreover, the longer a machine remains out of commission, the higher the costs incurred. To minimize downtime and its associated expenses, regular maintenance schedules must be implemented to detect and address potential issues before they escalate.
Replacement Parts and Supplies
Another substantial cost of machinery maintenance is the expense of replacement parts and supplies. Over time, machinery components wear out and need to be replaced to ensure optimal performance. The cost of these replacement parts can vary depending on the type of equipment and the complexity of the components. Additionally, regular maintenance also requires supplies such as lubricants, filters, and cleaning agents, which contribute to the overall cost of upkeep.
Labor Costs
Labor costs are a significant component of machinery maintenance expenses. Skilled technicians are needed to perform routine maintenance tasks, conduct inspections, and troubleshoot issues. The wages of these technicians, along with any additional training or certifications required, add to the overall cost of keeping machinery in good working condition. Moreover, emergency repairs or after-hours maintenance can incur higher labor costs, further emphasizing the importance of proactive maintenance practices.
Equipment Upgrades and Retrofits
As technology continues to advance, machinery maintenance costs can also include equipment upgrades and retrofits. Upgrading machinery to newer models or retrofitting existing equipment with modern components can improve efficiency, productivity, and safety. However, these upgrades come with a price tag that must be factored into the overall maintenance budget. While the initial investment in upgrades may be substantial, the long-term benefits in terms of performance and longevity can outweigh the costs.
Training and Education
Ensuring that maintenance personnel are adequately trained and up-to-date with the latest industry practices is essential for effective machinery maintenance. Training programs, workshops, and certifications can incur additional costs but are crucial for maintaining a skilled workforce capable of handling complex machinery issues. Investing in ongoing education for maintenance staff can lead to improved equipment reliability, reduced downtime, and ultimately, lower maintenance costs in the long run.
Environmental and Regulatory Compliance
In today’s increasingly regulated environment, machinery maintenance costs also include ensuring compliance with environmental and safety regulations. Proper disposal of hazardous materials, adherence to emissions standards, and compliance with workplace safety regulations are all factors that contribute to the overall cost of maintenance. Failing to meet these regulatory requirements can result in fines, penalties, and reputational damage, making adherence to compliance standards a necessary investment.
Conclusion: The Value of Proactive Maintenance
In conclusion, while the costs associated with machinery maintenance may seem daunting, they are a necessary investment in ensuring the longevity and efficiency of equipment. By implementing proactive maintenance practices, businesses can minimize downtime, extend the lifespan of machinery, and reduce overall maintenance expenses in the long term. Prioritizing regular inspections, preventive maintenance, and staff training can ultimately lead to cost savings, improved operational efficiency, and a competitive edge in today’s fast-paced business landscape.