What Are the Safety Guidelines for Machinery Maintenance
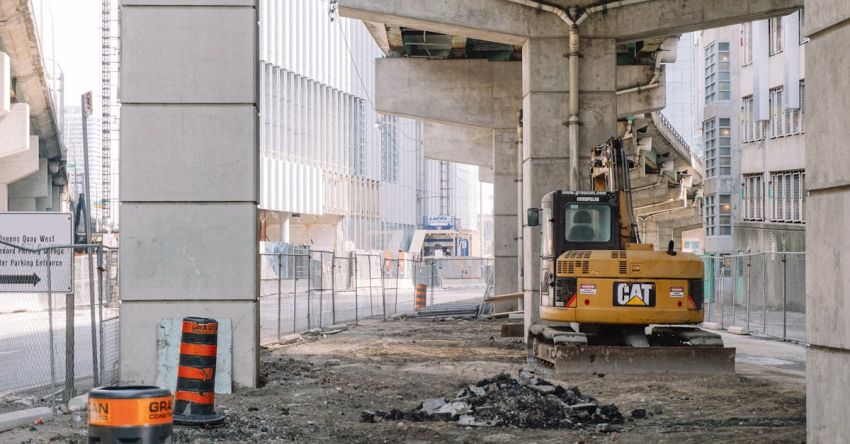
Ensuring the safety of workers is paramount in any industrial setting, especially when it comes to machinery maintenance. Proper maintenance not only prolongs the life of equipment but also reduces the risk of accidents and injuries. To achieve this, it is essential to follow specific safety guidelines that help create a secure working environment for all individuals involved in machinery maintenance operations.
Understanding Machinery Hazards
Before embarking on any maintenance task, it is crucial to identify potential hazards associated with the machinery. These hazards can vary depending on the type of equipment being worked on, but common risks include electrical shocks, moving parts, high temperatures, and falling objects. By conducting a thorough risk assessment, maintenance personnel can develop a comprehensive safety plan that addresses these hazards effectively.
Personal Protective Equipment (PPE)
The use of appropriate personal protective equipment is non-negotiable when it comes to machinery maintenance. Workers must wear the necessary gear such as safety goggles, gloves, hard hats, ear protection, and steel-toed boots to protect themselves from potential injuries. PPE should be selected based on the specific hazards present in the maintenance environment and should be worn at all times during maintenance tasks.
Lockout-Tagout Procedures
One of the most critical safety guidelines for machinery maintenance is the implementation of lockout-tagout procedures. This involves disconnecting the machinery from its power source and ensuring that it cannot be turned on accidentally while maintenance is being performed. Lockout-tagout procedures help prevent unexpected energization of equipment, which can lead to serious accidents. All workers involved in maintenance tasks should be trained on lockout-tagout procedures and strictly adhere to them at all times.
Proper Training and Supervision
Proper training is essential for all personnel involved in machinery maintenance. Workers should be trained on the specific maintenance procedures, safety protocols, and emergency response measures before they are allowed to work on any equipment. Additionally, having experienced supervisors oversee maintenance operations can provide an extra layer of safety by ensuring that tasks are being performed correctly and safely.
Regular Inspections and Maintenance
Regular inspections and maintenance of machinery are crucial for ensuring that equipment is in good working condition and safe to operate. Any signs of wear and tear, damage, or malfunction should be addressed immediately to prevent accidents. Establishing a routine maintenance schedule and conducting thorough inspections can help identify potential issues before they escalate into safety hazards.
Safe Handling of Tools and Equipment
Proper handling of tools and equipment is essential to prevent injuries during machinery maintenance. Tools should be used for their intended purpose and stored in designated areas when not in use. All equipment should be inspected for defects before use, and damaged tools should be replaced immediately. Workers should also be trained on the correct handling techniques to minimize the risk of accidents.
Emergency Response and Communication
In the event of an emergency, quick and effective communication is key to ensuring the safety of all personnel involved in machinery maintenance. Emergency response procedures should be clearly outlined, and all workers should be familiar with the steps to take in case of an emergency. Additionally, having communication devices such as two-way radios or emergency alarms can help coordinate a swift response in critical situations.
Conclusion: Prioritizing Safety in Machinery Maintenance
In conclusion, adhering to safety guidelines is essential for maintaining a safe work environment during machinery maintenance operations. By understanding machinery hazards, using proper personal protective equipment, implementing lockout-tagout procedures, providing adequate training and supervision, conducting regular inspections, handling tools and equipment safely, and establishing effective emergency response protocols, organizations can create a culture of safety that protects workers and minimizes the risk of accidents. Prioritizing safety in machinery maintenance not only safeguards the well-being of employees but also enhances overall productivity and efficiency in the workplace.